Pressure Rating
The trend in today's mobile hydraulic systems is toward more complexity and higher working pressures. More pressure means more efficiency for the user of a hydraulic system, but more challenges for the system's manufacturer who typically uses components like seals, valves, and manifolds.
Additionally, as hydraulic systems become more complex and compact, manifolds have progressed from simple blocks with 5-6 ports to more intricate components with the ability to accommodate a dozen or more connections.
Until recently, pressure ratings for hydraulic manifolds made from ductile iron were based on book values and conservative theoretical calculations, making design engineers reluctant to specify it in lieu of steel for applications involving more than 5,000psi.
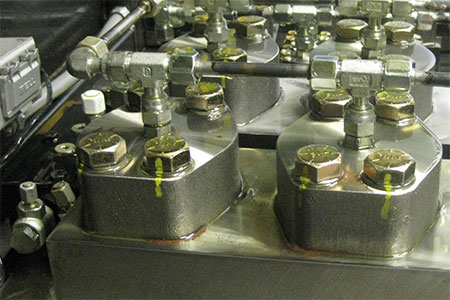
Dura-Bar is now pressure rated to 6,500 psi and conforms to NFPA standard T2.6.1 R2-2000
Verified Rated System Pressure*: 6,500 psi
Bore Size (in) | Minimum Allowable Wall Thickness (in) |
---|---|
0.5 | 0.050 |
1.0 | 0.100 |
2.0 | 0.150 |
* Method of verifying the rated fatigue pressure (or establishing the rated burst pressure; or both) of the pressure containing envelope conforms to NFPA/T2.6.1 R2-2000, Fluid power components - Method for verifying the fatigue and establishing the burst pressure ratings of the pressure containing envelope of a metal fluid power component, for the values, categories and special conditions (if any) as specified. The configuration shown has an RFP = 44.82 MPa (6,500 psi), category C/90/ where k0 for ductile iron = 0.14.
Testing, verification, and rating performed by the Fluid Power Institute at the Milwaukee School of Engineering.
Dura-Bar's superior machinability also comes into play by facilitating drilling, and with little or no deburring it can reduce the overall cost to produce a manifold.